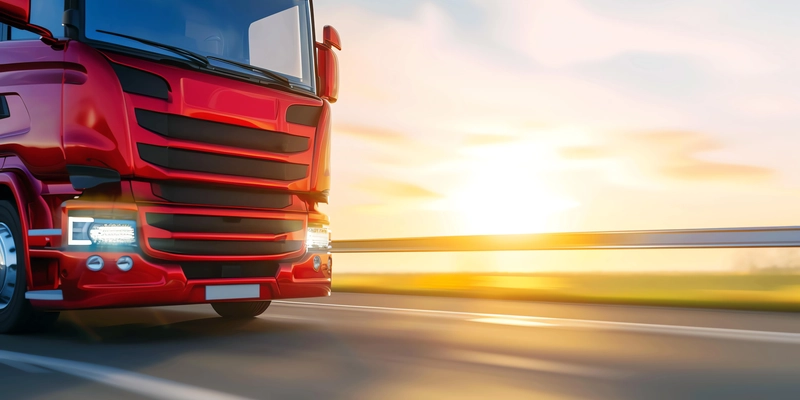
The Challenge
A major logistics company running deliveries across multiple U.S. states faced a growing problem: its fleet management system was stuck in the past. With 350+ vehicles on the road and warehouses in multiple locations, they relied on old-school methods—manual logs, scattered third-party tools, and too many phone calls.
As their business grew, so did their headaches:
✅ Too much manual work – Dispatchers and drivers wasted time on calls instead of focusing on deliveries.
✅ Unplanned breakdowns – Last-minute repairs caused delays, lost revenue, and unhappy customers.
✅ Zero real-time visibility – Without live tracking, optimizing routes and scheduling maintenance was a guessing game.
✅ Customer dissatisfaction – Missed deliveries meant lost business and a dented reputation.
They needed a complete digital revamp—fast. That’s where Yalantis stepped in.
The IoT-Powered Solution
Yalantis built an intelligent fleet management system that gave the company real-time control over its operations. Here’s how:
1️⃣ Smart IoT Sensors for Live Monitoring
Equipped the fleet with connected sensors to track everything from vehicle health to road and fleet conditions monitoring. Key metrics included:
🔹 Location tracking – Know where every truck is, in real time.
🔹 Tire pressure monitoring – Reduce blowouts and prevent accidents.
🔹 Engine health diagnostics – Catch small issues before they become big problems.
🔹 Load sensors – Ensure trucks aren’t overloaded or underutilized.
🔹 Proximity alerts – Reduce collision risks and improve safety.
2️⃣ A Scalable Cloud-Based System
To handle non-stop data from hundreds of vehicles, Yalantis built a microservices-based cloud platform. This allowed the company to:
✔️ Process real-time sensor data without delays.
✔️ Scale effortlessly as operations grew.
✔️ Maintain high performance with zero downtime.
They powered the system using AWS, integrating:
💡 AWS IoT Core for secure, instant data transfer.
💡 AWS Lambda for automated cloud processing.
💡 AWS Kinesis for handling massive amounts of fleet data.
💡 AWS IoT Fleet Hub for live monitoring and alerts.
3️⃣ Predictive Maintenance & AI Insights
Instead of waiting for a truck to break down, the system predicted failures before they happened. AI-driven analytics:
📊 Monitored real-time data and identified warning signs.
📊 Triggered alerts when performance dropped.
📊 Scheduled maintenance proactively—reducing emergency repairs.
With Amazon QuickSight, fleet managers got powerful dashboards with insights on vehicle health, fuel efficiency, and cost trends—all in one place.
4️⃣ Easy-to-Use Digital Interfaces
Different teams needed different tools, so Yalantis built:
📌 A fleet manager dashboard – Live tracking, route planning, and performance analytics.
📌 A driver mobile app – Trip logs, automated updates, and instant communication.
📌 A customer portal – Real-time shipment tracking and notifications.
📌 A support team hub – Issue resolution and logistics management.
The Results: A Fleet That Runs Smarter & Faster
By upgrading to an IoT-driven fleet management system, the company saw real, measurable improvements:
🚀 1.5x faster deliveries – Smarter route planning meant shorter transit times.
💰 Up to 40% lower costs – Preventative maintenance and fuel efficiency saved money.
📈 50% higher operational efficiency – Digital workflows replaced paperwork and manual tracking.
🔧 Fewer breakdowns & delays – Predictive analytics improved vehicle uptime.
🙌 Happier customers – Reliable deliveries boosted trust and retention.
Now, the company isn’t just keeping up with the competition—they’re setting the new standard for smart, connected fleet management.