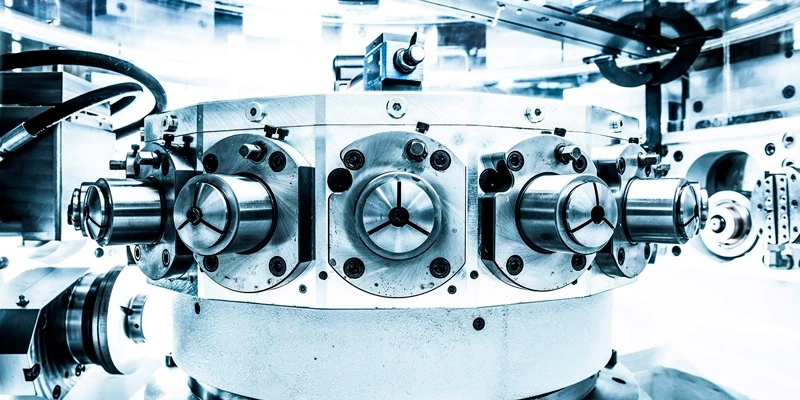
The Challenge: Aiming for Smarter Maintenance of Machines
An innovative engineering firm, known for its precision rotary transfer machines, faced a tough hurdle. These machines, crucial for producing high-quality workpieces, required meticulous maintenance. Planned shutdowns. Precise coordination. It was a time-consuming, resource-heavy process that demanded a better way forward.
To tackle this, the firm launched its own service company. Teams of technicians were dispatched to customer sites to inspect machines, assess spindle conditions, and replace components when necessary. Maintenance was carried out according to fixed schedules, but the process was labor-intensive and rigid.
The need for a smarter solution became apparent. The vision? A digital maintenance system powered by IoT technology. This system would automate data collection directly from machine spindles and feed it into an application. With this, service technicians could pinpoint faults and anticipate part replacements before even setting foot on-site. Efficiency would be redefined.
To make this vision a reality, the firm teamed up with BLUE-ZONE GmbH, a company boasting over two decades of expertise in automation and digital transformation. Together, they set out to craft a cutting-edge, industrial iot maintenance solution.
The Solution: Smarter Insights, Fewer Breakdowns
The partnership birthed a transformative software solution. Developed by BLUE-ZONE, it harnessed IoT technologies to deliver real-time monitoring and analysis. The aim was clear: detect anomalies early, reduce unplanned downtime, and optimize every aspect of maintenance.
Collecting Vital Data with Sensors
Strategically installed sensors became the lifeblood of the solution. These devices measured critical parameters such as spindle speed, torque, temperature, feed speed, and even the precise XYZ positioning of components. This data became the foundation for detailed machine diagnostics.
To ensure seamless adoption, the solution was designed hand-in-hand with the firm’s specialist teams. Existing workflows were preserved, sparing businesses from disruptive overhauls. Instead, this advanced system enhanced current processes.
Monitoring Machines in Real Time
The sensor data flowed through a gateway, finding its way to either in-house servers or preferred cloud platforms. A customizable dashboard gave users a clear, live view of machine health, enabling them to spot and address issues before they spiraled into costly breakdowns.
By aligning maintenance with real needs instead of rigid schedules, downtime was slashed. This data-driven approach not only reduced costs but also boosted machine availability and overall equipment effectiveness (OEE).
Unlocking Insights for Better Machines
Continuous iot monitoring brought more than operational efficiency—it opened doors for innovation. By analyzing machine data, engineers pinpointed design weaknesses, paving the way for more durable, efficient, and user-friendly future machines. The integration of data into product development created a virtuous cycle of improvement.
Automatic software updates were another game-changer. These updates delivered security enhancements and new features, ensuring users always operated with the latest tools to optimize performance.
The Result: Turning Data into Competitive Advantage
The IoT-driven solution empowered the innovative engineering firm to revolutionize its maintenance processes. Machines were now monitored continuously, anomalies detected early, and maintenance streamlined. The payoff? Drastically reduced downtime, smarter maintenance cycles, and enhanced machine performance.
But this was just the beginning. Future upgrades aim to unlock even more potential:
- Remote configuration: Machines across global production networks can be adjusted centrally.
- ERP integration: Seamless data flow into business systems ensures tighter integration between production and planning processes.
- Predictive maintenance: Advanced algorithms will predict component wear, enabling timely interventions and further cutting costs.
This solution exemplifies how IoT technologies are reshaping industries. By bridging the gap between data and decision-making, it drives innovation, boosts efficiency, and sets the stage for long-term success.